In order to ensure product quality, Our Company carries on the strict inspection and examination during the products producing process.
1. Raw material testing
1.1 Each raw material is strictly inspected to ensure that it is a qualified product
No. |
Inspection and test content |
Inspection and testing standards |
1 |
Chemical composition analysis and quality inspection of wet end parts raw materials |
Enterprise standard (metal raw materials for casting) (auxiliary raw materials for casting) (molding raw materials) / Enterprise standards (technical condition of pump cast iron parts ) / enterprise standards (anti-wear white cast iron parts) |
2 |
Chemical composition analysis and quality inspection of shaft raw materials |
National standards |
1.2 Mechanical performance report of shaft
No. |
Inspection and test content |
Inspection and testing standards |
3 |
Mechanical performance report of shaft |
National standards |
4 |
Nondestructive Inspection Report of shaft |
National standard |
2. Inspection of casting process
2.1 Sand Mixing process (Inspection of foundry sand)
2.2 Modeling process(Inspection of mold core)
2.3 Melting casting process(Pre-furnace operation record) (casting records) (melting casting records)
2.4 Heat Treatment Process (Wear - resistant white castings and cast iron heat treatment process records)
2.5 Mold dismantling, sand shakeout (Casting cleaning process records)
3. Inspection of machining process
3.1 Dimension Self-Inspection, Mutual inspection, First inspection; hardness
tester hardness testing
3.2 Impeller dynamic and static balance detection: inspection standard ISO1940
impeller balance G2.5
3.3 Pump pressure test: the standard pressure test 1.5 times of the design
pressure
4. Combined performance test and cavitation test
(Flow, head, efficiency, vibration, noise, cavitation): test standard ISO9906-1999
5. Final inspection
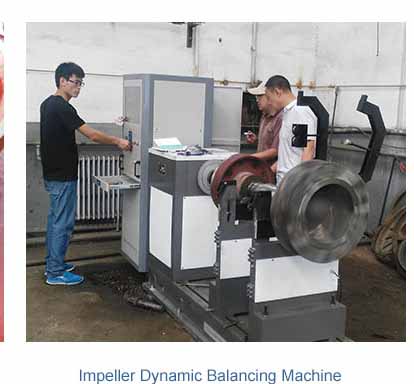
impeller dynamic balancing test
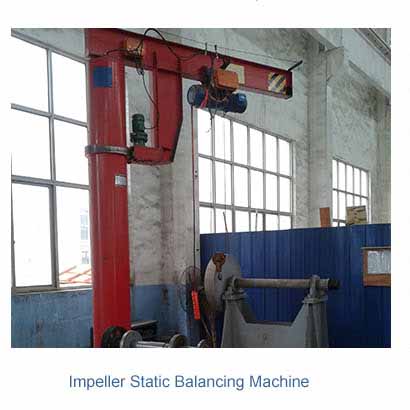
impeller static balancing test